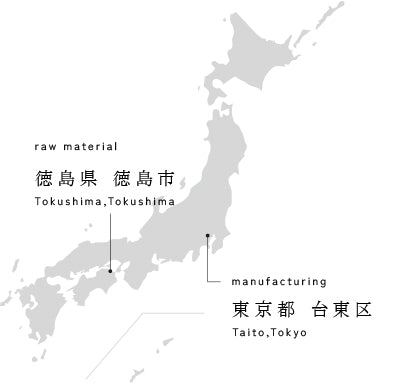
The color "Japan Blue"
Indigo dye
Indigo dyeing is done by fermenting and dyeing using "sukumo" made from Polygonum indigo in Tokushima Prefecture. Indigo fermentation liquid is highly alkaline, and leather is weak to alkaline, so a special indigo fermentation liquid with weaker alkalinity is made for leather and dyeing. This liquid spoils easily and has a pale color, so it must be dyed with care, and it takes more time and effort than indigo dyeing fabric. In recent years, indigo-dyed leather dyed with chrome tanning has become more common, but tannin-tanned leather has low resistance to alkali and water, making it very difficult to dye, so tannin-tanned indigo-dyed leather is very valuable. Sukumo is made by adding water to dried indigo leaves and fermenting them. The harvested indigo is dried and crushed by hand while kneading. At this time, stems and debris are removed, leaving only the leaves. The crushed leaves are mixed well with water and fermented, matured for about three months, and dried in the shade. The pH of the resulting indigo is adjusted to an alkaline level, and the process of fermenting it is called "aidate." Through these various intricate craftsmanship steps, a deep, vibrant indigo color is achieved.
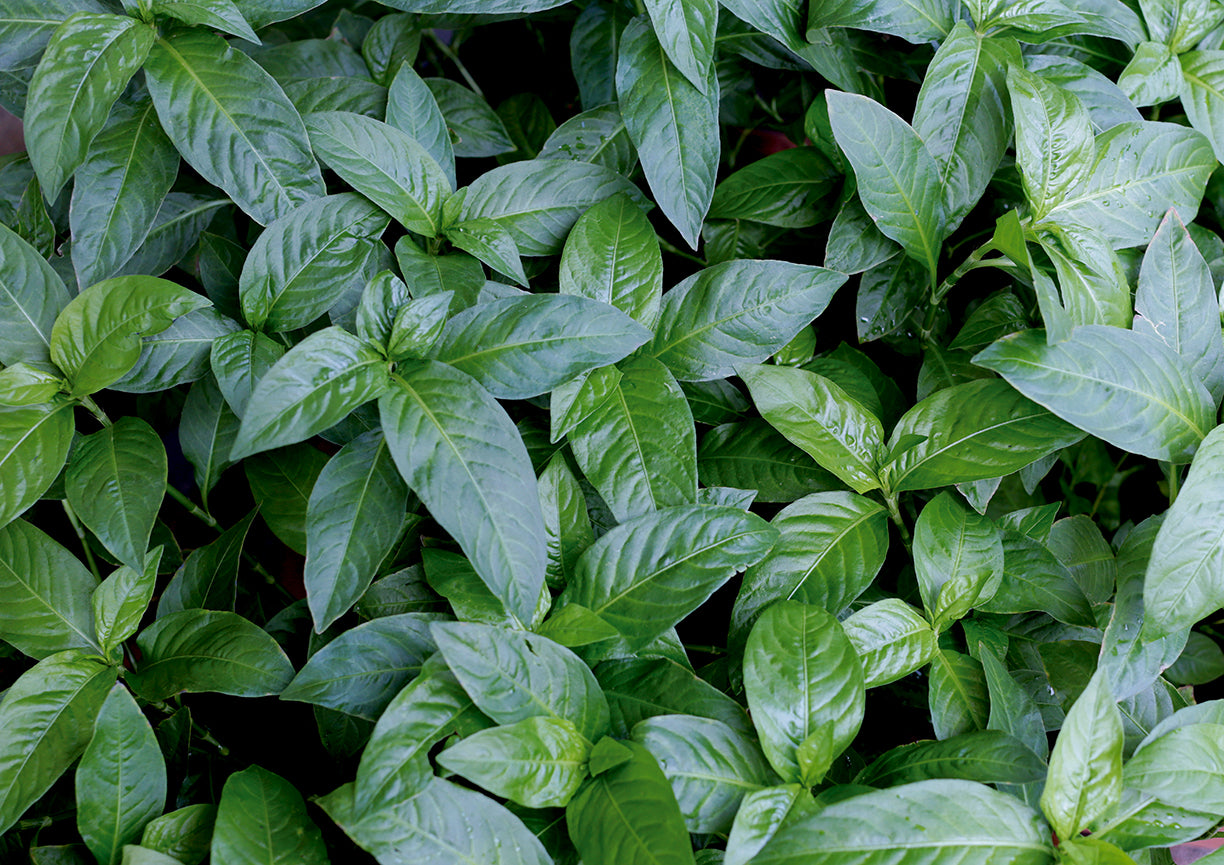
Indigo from Tokushima Prefecture has been popular since the Edo period
Indigo dyeing was introduced from China in ancient times, and was popular among the common people in the Edo period. It has a strong antibacterial effect, and dyed clothes were used to prevent skin diseases and poisonous insects. There are various varieties such as Kojoko, Hyakukan, and Senbon, and it is currently grown in Tokushima, Miyazaki, Hokkaido, etc., but production is decreasing year by year. At "te saho", we mainly use fermented indigo plant of Kojoko from Tokushima, which has been praised as the finest since the Edo period, and we ferment and dye it.
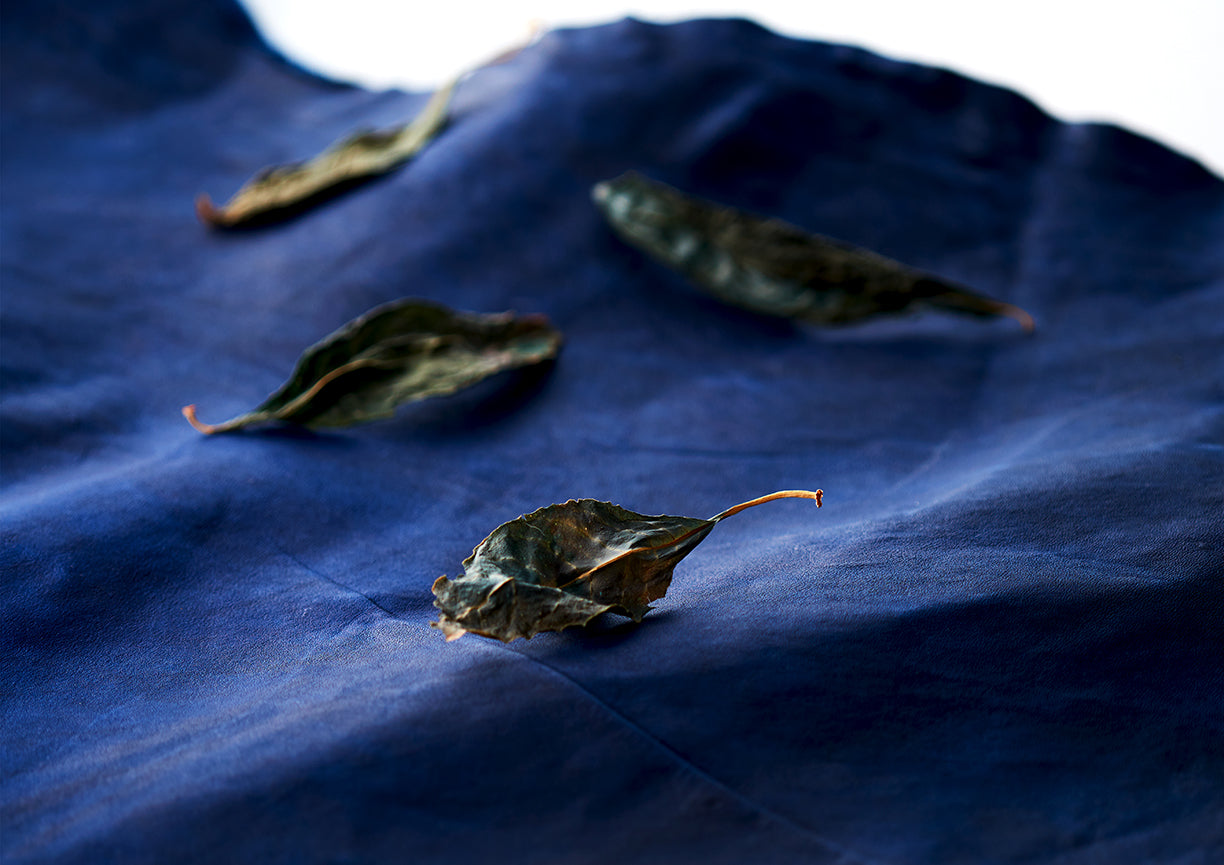
Indigo dye
Indigo plants contain a substance called indican. When the plant's cells are destroyed, the enzymes in the leaves cause the indican to oxidize easily, and when it comes into contact with air, it oxidizes and becomes the indigo pigment that gives the plant its indigo color.
Indigo dye is a pigment that is insoluble in water. This insoluble indigo dye is made soluble in an alkaline aqueous solution using an oxidation-reduction reaction, which is called "indigo dye preparation." Indigo dye preparation using the action of microorganisms is called "fermentation preparation," while indigo dye preparation using chemicals is called "chemical preparation." The alkaline aqueous solution used in the indigo dye preparation is absorbed into the leather and then oxidized again within the fibers, causing the indigo dye to develop an indigo color.
Line up
100% natural indigo dyeing that brings together the skills and experience of artisans
Most of the indigo-dyed leather on the market uses synthetic indigo and solvents, which makes it easier to dye it to the desired deep color.
At te saho, we use tanned leather as the base leather and then dye it with indigo (sukumo) using 100% natural dyes to create truly natural indigo-dyed leather.
Since this leather is made from natural leather and natural dyes, the color may vary slightly depending on when the plants are harvested.
However, this is a color that can only be found at that time, making it a truly one-of-a-kind leather full of unique individuality.
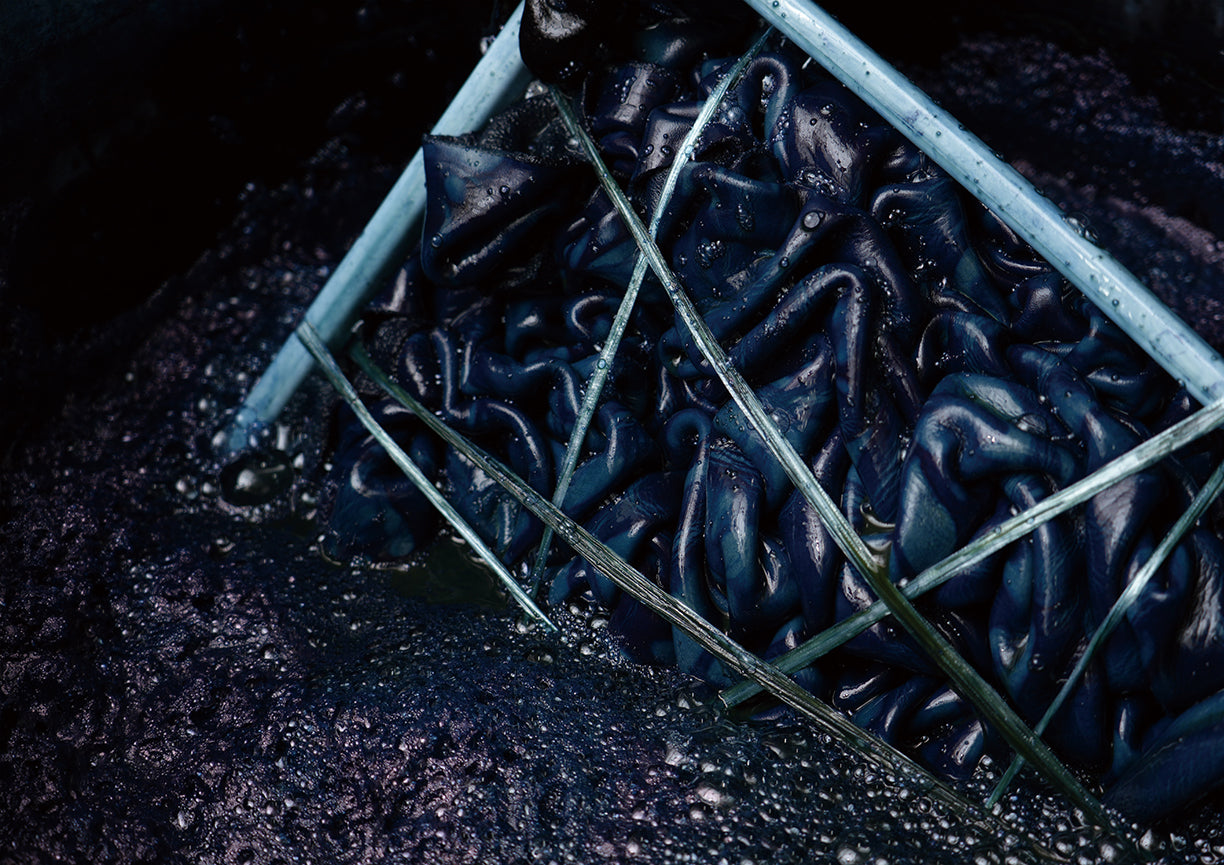
The difficulty of indigo dyeing leather
Indigo dyeing is done in a workshop in Taito, Tokyo, using "sukumo" from Tokushima Prefecture, which is made from Japanese knotweed. Normally, indigo fermentation liquid is highly alkaline, and leather is weak to alkaline, so a special indigo fermentation liquid with a weaker alkali is made and dyed. Chrome-tanned indigo-dyed leather is now becoming available, but tannin-tanned leather has poor resistance to alkaline and water, making it very difficult to dye and a valuable indigo-dyed leather.
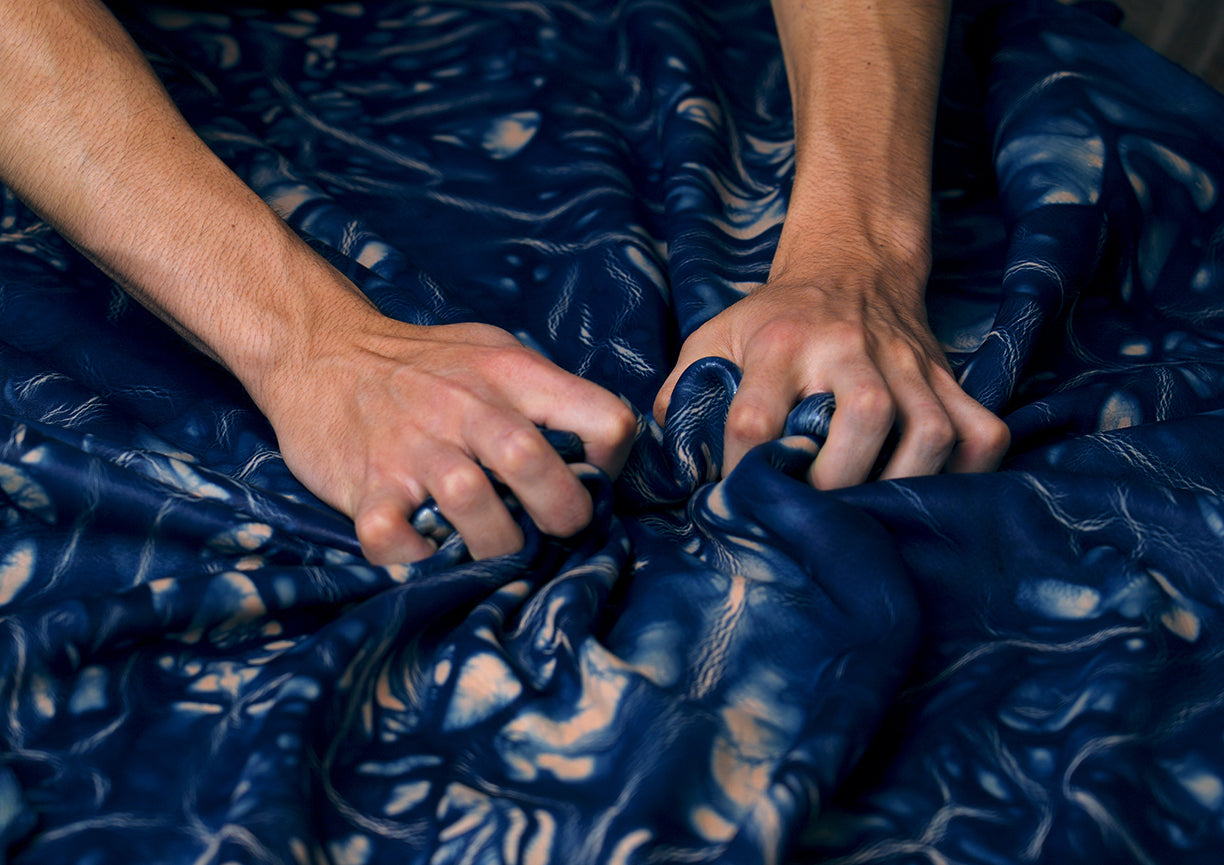
Adjusting the color of a once-in-a-lifetime encounter
"Sukumo" is made by adding water to dried indigo leaves and fermenting them. The harvested indigo is dried and crushed by hand while being rubbed. At this time, stems and debris are removed, leaving only the leaves. The crushed leaves are mixed well with water and fermented. It is left to mature for about a month and then dried in the shade. The resulting sukumo is mixed with lye and lime to adjust the pH to an alkaline level, and wheat bran, which acts as nutrients for the microorganisms, as well as sake and glucose, are added, and the indigo dye solution is made by fermenting.
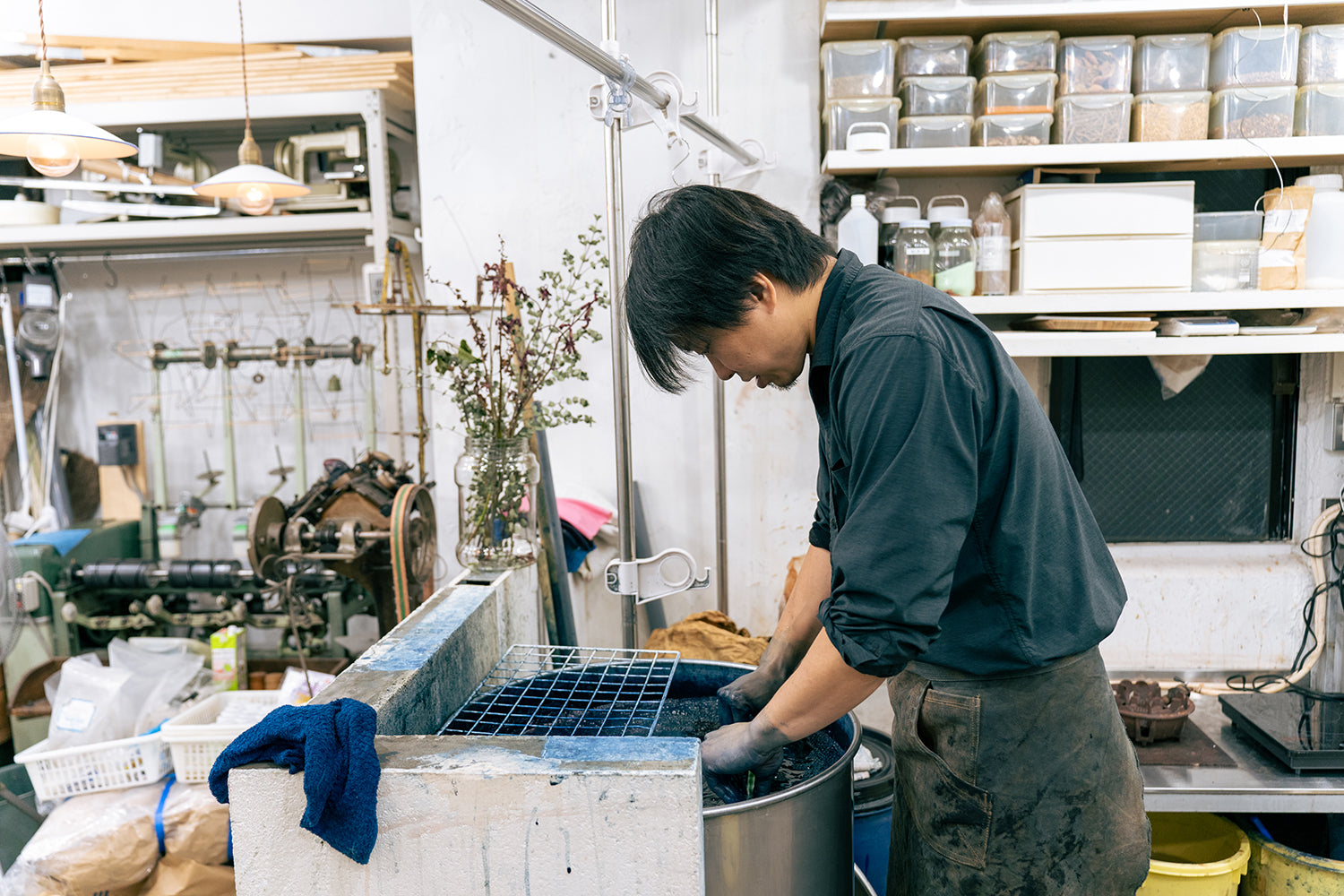
Environmentally friendly dyeing frequency
The intensity of the indigo dye color changes depending on the number of times it is dyed, the weather of the day, and other environmental factors. It is dyed repeatedly about 15 times with indigo blue and about 25 times with indigo blue.
Until leather is made
-
1. Indigo dyeing (fermentation)
Using "sukumo" produced in Tokushima, natural lye, lime, and shell ash are used to adjust the alkalinity and ferment the dye to create indigo dye solution (indigo dyeing).
*Polygonum indigo is a dye plant unique to Japan (said to have been created during the Edo period), harvested in the summer, with the first and second harvested leaves said to be good for dyeing. The harvested leaves are fermented for about three months to produce sukumo, and it is said that the leaves that are stored for as long as possible after production are best suited for dyeing. Currently, there are only five indigo masters (Awa Indigo Manufacturing Technique Preservation Society) who make Awa indigo in Tokushima. The sukumo that the indigo masters have made using traditional methods is used to make dye liquid using the traditional method of natural lye fermentation.
-
2. Adjust the dye solution
The dye solution made for dyeing leather is adjusted. After a few days, sugar is added such as sake to strengthen the reducing fermentation, and the alkali is reduced to a level that will not damage the leather.
-
3. Creating a tie-dye pattern
The leather is soaked in lukewarm water for a few days to soften it, and then squeezed to apply the pattern. Carefully create pleats to create as even a mottled pattern as possible, and secure the squeezed leather in a basket that fits the size of the leather using string. The key is to squeeze the leather while thinking about how to get an even pattern over the entire surface.
-
4. Dyeing (permeation and oxidation)
The fabric is soaked in the dye solution to allow the indigo to soak in thoroughly. Once soaked, it is removed from the solution and exposed to air to oxidize and develop color. This process is repeated about 10 to 30 times depending on the color strength and shading pattern.
-
5. Neutralization and re-tanning
Between dyeing processes, vegetable tannins such as chestnut and mimosa are added to create texture.
*When dyeing a large number of items, the bacteria in the indigo dye solution will decrease (there will be fewer enzymes), and the dye will become thin and oxidize, so it will be necessary to add bran (wheat husks) and sugar again, warm it up, grow it, and prepare the dye solution over several days before dyeing. To prevent the leather from being damaged again after dyeing, the leather will be soaked in a solution of dissolved vegetable tannin to add more tannin.
-
6. Add fat and adjust the texture
What's even more important is to soak the leather in a liquid made by emulsifying fish (especially cod) or cow oil that is suitable for the leather and dissolving it in water, to give it a moist texture.
-
7. Rinse with water
Rinse thoroughly under running water to remove excess indigo and lye from the surface.
-
8. Drying and texture development
After kneading thoroughly, the fabric is hung to dry. After drying, it is kneaded some more and oil is added to give it the final texture.

Dyeing
Masato Komuro
Born in Fukuoka in 1983, he lives in Tokyo. He moved to Akizuki, Asakura City, Fukuoka Prefecture, where he was exposed to plant dyeing at his family's plant dyeing studio (Kobo Yumezaiku). He majored in dyeing and weaving at the Department of Crafts, Faculty of Fine Arts, Tokyo University of the Arts. While studying traditional techniques, he also explored new technical expressions such as plant dyeing leather. In 2007, he introduced whole garment knitting and mastered the techniques. In 2008, he started his own knitwear brand, "MAITO". In 2010, he established Might Design Works Co., Ltd. In the same year, he opened a directly managed store at 2k540 in Ueno, Taito Ward, Tokyo. In 2012, he opened an atelier shop in Kuramae, Taito Ward, Tokyo.
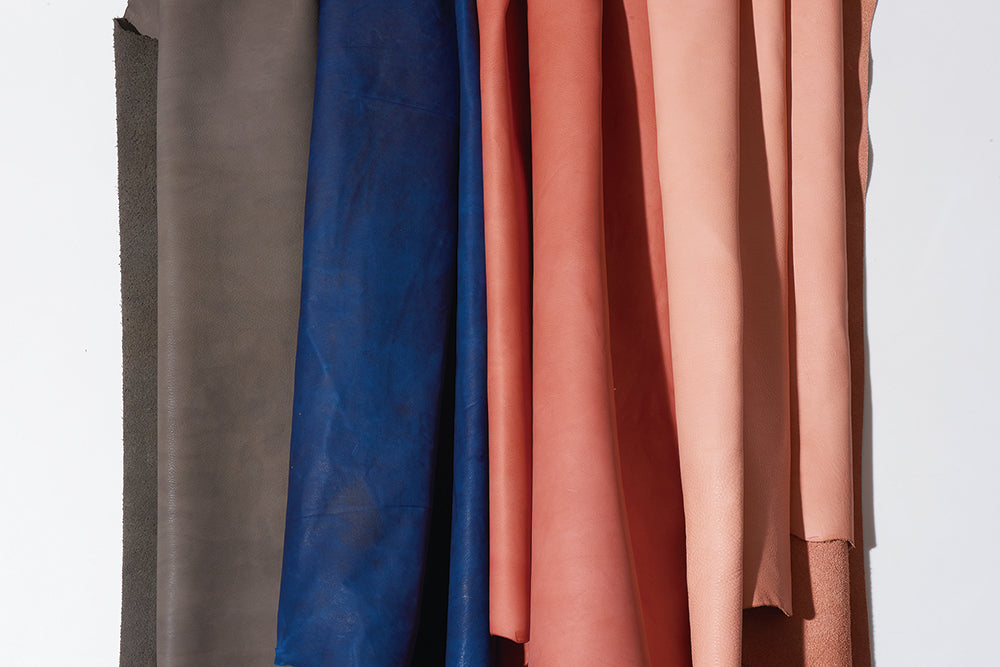
Botanical Leather®
Unlike plant dyeing, which uses chemical dyes, Botanical Leather® is dyed using only natural dyes made from plants, without the use of chemical dyes. This is why it is characterized by its unique, gentle colors that are kind to the environment and people. Plant dyeing, which produces colors that are full of life, is a complex combination of various factors such as the concentration of the dye, the temperature difference between inside and outside the workshop, the dyeing time, and the way the leather is moved, so even if it is dyed with the same dye, the color will be different. In addition, the plants and trees that are the raw materials are different even if they were cut today and two weeks later, or this year and next year. In other words, you will never encounter the same color twice. It's a once-in-a-lifetime encounter, so to speak. This is also one of the charms of plant dyeing.
Wear this leather
-
Card case / botanical leather® indigo dye / spotted / cowhide
BAM-P-01Regular price €274,95 EURRegular priceUnit price per